University News Last updated 01 October 2021
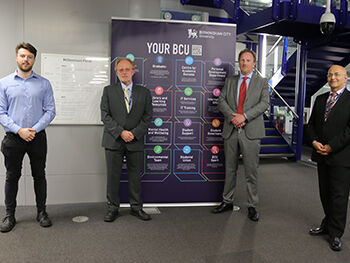
Birmingham City University has made a million pound investment into new hi-tech engineering and computing equipment – thanks to funding secured by a city-wide technology partnership.
The £1.1 million financial boost was secured through the Greater Birmingham and Solihull Institute of Technology (GBSIoT), in which the University is an anchor partner and which is one of several government-backed collaborations between local employers and further and higher education providers set up to deliver technical training across England.
The Department for Education provided £808k of the total funding package, which the University has used to develop an electric vehicle (EV) test cell and an additive manufacturing machine – commonly known as a 3D printer.
The remaining £295k – from the Greater Birmingham and Solihull Local Enterprise Partnership (GBSLEP) – has gone towards technologies to improve student connectivity, the University’s Formula Student workshop, reverse engineering applications, material testing and electronics equipment for prototyping and production line simulation.
Professor Julian Beer, Deputy Vice-Chancellor, Birmingham City University and Board Director of the Greater Birmingham and Solihull Institute of Technology, said:
“We are delighted to have received this funding, which we have put to good use by obtaining specialist apparatus that will enhance both our teaching and research capabilities, all the while benefiting our students and strengthening our already solid links with industry.”
Representatives from the Department for Education, and the GBSIoT, as well as industry leads visited the University’s Faculty for Computing, Engineering and the Built Environment earlier this month to view the new facilities and equipment.
The delegation also learned more about the University’s strategy for tackling future challenges in manufacturing, engineering and other hi-tech industries. The plan encompasses a comprehensive research programme across different science, technology, engineering and mathematics disciplines alongside the arts.
Working in partnership with a range of businesses, this work will also help drive the University’s STEAM project which places the arts at the heart of traditional technical subjects and will complement the opening of the University’s new STEAMhouse facility which will be home to its School of Computer and Digital Technology.
Central to the University’s future-proofing work is ensuring that students, researchers and industry links have access to state-of the-art technologies such as the EV test cell and metal 3D printer, obtained thanks to the investment made by the Department for Education.
Professor Beer added:
It’s essential therefore that we have the right tools at our disposal and likewise – as these are big issues that affect everyone – are able to work collaboratively with industry partners for our mutual benefit. We can achieve all of this through our association with the Institute of Technology and we’re very pleased to be part of this.”
The EV test cell is a vital tool in aiding the transition to low-carbon transportation as it enables the development and trialling of systems and components against automotive industry specifications and regulations.
The additive manufacturing machine can convert designs into prototype physical models using considerably less time and resource than traditional manufacturing methods thus boosting the potential for greater innovation across a range of industries from aerospace and automotive to biomedical science.
Professor Hanifa Shah, Pro-Vice-Chancellor and Executive Dean of the Faculty of Computing, Engineering and the Built Environment, said:
“New and emerging technologies are a strategic priority for Birmingham City University and this investment supports our continued dedication to skills and research in UK engineering and manufacturing businesses.
“In particular the addition of an electric vehicle test cell – one of but a few at universities nationally – comes at an appropriate time with new challenges placed on manufacturers to respond to the government’s mandate for transition towards zero emission vehicles and to growing domestic demand for electric cars.”
The University is also widening its teaching provision to include delivery of degree apprenticeships with employers, short courses and continuing professional development for those already working in the technology sector as well as traditional university degrees.
Adam Burgoyne, NPI & Quality Engineer at precision stamping specialists C. Brandauer & Co Ltd, is undertaking a Degree Apprenticeship in Manufacturing, developed by the University and supported by GBSIoT. He said:
“I’m extremely grateful to be backed by my company Brandauer to develop my knowledge and skills through the University’s Degree Apprenticeship. I can’t wait to get hands-on time with their new cutting-edge technologies and to learn from their experts.”