Birmingham City University (BCU) have joined multidisciplinary consortium to develop a new platform for design for manufacture and assembly home, known as DfMA house. The platform enables house design to be faster to construct, economical to build and low impacts to the environment. Whilst meeting the Government’s set targets and tackling the housing shortage at hand, DFMA house also addresses the frustrating logistical challenges associated with restricted area and small space.
The platform includes the use of a ‘kit-of-parts’ approach is used to develop DfMA house. It is part of the output from an Innovate UK funded project “Collaborative knowledge-based DfMA approach to building cost-efficient, low-impact and high-performance houses” with an overarching aim to transform housing design and construction. 3 aspects are considered in the platform: (i) Design for Manufacture, (ii) Design for Assembly and (iii) Design for Life Cycle Performance.
To standardise and commodify the design and construction process, the DfMA house is broken down into pod units and panels units to suit various production needs and enable feasible and efficient project delivery.
Objectives
The Platform-based DfMA house optimises prefabrication by increasing automation potential and obtain benefits of off-site construction while allowing sufficient customisation of the house product. The following objectives have been developed:
- Enhance the manufacturing process of DfMA house by adopting a ‘kits-of-parts approach to minimise rework, production of waste and risks.
- Develop standardised pods units and panel units to boost automation, precision and quality of the manufacturing process
- Adopt best practices of site assembly, onsite storage and transportation to minimise physical efforts and logistical constraints
- Deliver design solutions that maximises energy efficiencies across the project’s lifecycle at a minimum whole life cost.
House prototype at built at Hadley’s factory developed using the DfMA platform
Consortium members
BCU team provides research and insight, particularly in defining the design criteria and the data requirements for the platform based DfMA house, and support the development of the design solutions. The knowledge generated from the platform development is programmed in a knowledge-based engineering tool. Key researchers of the project are:
- Dr Franco Cheung (Principal Investigator)
- Dr Abdel-Rahman Tawil
- Dr Edlira (Kalemi) Vakaj
- Panagiotis Patlakas
- Kudirat Ayinla
Industrial partners:
- Walsall Housing Group (whg) - one the largest providers of affordable and high-quality homes across the West Midlands region. They define the user requirements for the project.
- Hadley Group - a world-class engineering leader in cold roll forming technologies, specialise in producing light-weighted steel components, with exemplary fire resistance ratings and acoustic entrapment. They design the steel framework for the DfMA house.
- Northmill Associates - a design-led architectural firm, offering robust, client focused advice and building solutions. They lead the development of DfMA house design.
- QM systems - an innovative solution provider of automated test systems for production lines, robotics and bespoke engineering development. They evaluate the automation potential in the design for manufacture.
- Energy Systems Catapult (ESC) - a dedicated team of qualified engineers with a mission to unleash innovative solutions to decarbonise society and capture opportunities to minimise the ecological footprint. They assess the energy performance of DfMA house design.
Principles of the DfMA House Platform
DfMA house shall accommodate a number of house types such as detached, semi-detached and terrace units, and is flexible enough to adopt different offsite systems and production methods. The following categorise the upper limits for platform-based design:
- Spanning capability up to 5m
- Loading capacity for transportation up to 10 tonnes
- Storey height up to 3m
- Building height up to 2 storeys
- Ability to accommodate various levels (3 standards – Gold, Silver and Bronze – are defined with various services provisions)
- Ability to accommodate various offsite systems: i.e. panelised, volumetric and a combination of both systems (Pod and panel system)
- Ability to accommodate open or close kitchen design
- Ability to accommodate semi-automated line production or automated production methods
- Flexible for changes in the facade appearance e.g. timber boarding, brick and rendering as well as sizes and positioning of openings for windows and doors
Kit of parts for the DfMA House Platform
The DfMA house adopts a kit-of-parts approach which utilises a building repeatable platform to assemble and manufacture residential homes. The term kits-of-parts can be defined as a collection of object-oriented components that can fit together to achieve a variety of configurations and form a modular-based DfMA house. This can yield exponential benefits in terms of generating time and cost savings, whilst increasing the quality, flexibility in assembly and efficiency in manufacture. There are several key components of the DfMA house which uses an adaptable kits-of-part approach to increase practicality and speed of construction. This includes the following components:
- Carcass - Frame (panelised system), frame for Pods (volumetric system)
- Components - Windows and external doors, façade system, stairs, fittings and fixture
- Services systems - Hot and cold water, heating, solar and battery system, electricity system, telephone and TV distribution, lighting system, incoming data
- Interfaces - Lift cleats, plug-and-play system for lighting, electricity and to fix the two pods together, pod system for windows and doors, cladding system
- Sub-assemblies - Floor and wall panels, pods, roof
Design for Manufacture
Design criteria
Table 2 summarises all of the design criteria incorporated across 4 design levels: (i) House; (ii) House Frame; (iii) Central Pod Units and (iv) Wall Panel Units. The criteria’s form a basis to create effective repetitious standardised design units that are fit-for-purpose, cost effective and durable. Not only will DfMA house encompass these quality, but there is also stringent compliance to Building Standards & Regulations and high supply chain integration across the project life-cycle to amplify innovation and add value. Flexibility is also factored, so feasible design configurations can take place to meet the ‘needs’ and ‘wants’ of various clients. Ultimately, meeting the criteria will help establish effective design solutions for manufacture, leading to a successful DfMA home.
Table 2: Design for Manufacture Design Criteria
|
House |
House Frame |
Central Pod Units |
Wall Panel Units |
Design criteria |
|
|
|
|
Design solution
1) DfMA house
The DfMA house is designed to meet the requirements for two separate systems: panelised and volumetric systems. The panelised system for DfMA house is a 2-dimensional system that comprises of floor and wall panels for production in the factory. The factory-manufactured panels are then transported for onsite assembly to form part of the carcass of the DfMA house. The volumetric system for DfMA house is a 3-dimensional system that comprises of 6 pods with each comprising wall and floor panels, a pod frame, fittings, services installation, and potentially finishes (See Figure 1). In the development of the design, a third option, i.e. the pod and panel system combining central pods and panels (floor and wall panels for the other parts of the building), has been developed to meet the need for more stringent site and/or transportation requirements yet maximise the offsite production potential (See Figure 2).

Figure 1: DfMA house built by volumetric method comprising 6 pods
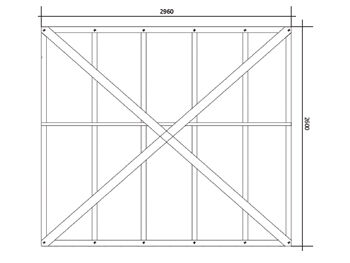
Figure 3: Wall Panel Unit Frame
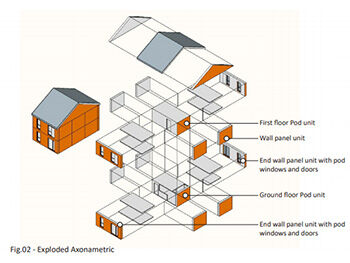
Figure 2: Exploded Axonometric of the pod and panel system
2) House frame
The panel frame is designed to be compatible for the pod unit in the volumetric system and the product in a panelised system to allow for standardisation and reproducibility. There is also studwork at appropriate centres to allow internal linings and external wall finishes to be fitted accordingly (See Figure 3 above). Furthermore, the material for the frame is constituted of lightweight cold rolled steel with similar steel profiles and load bearing capacity to increase uniformity and allow feasible inventory management, distribution and storage of stock.
3) Central pod units
The central pod units are the heart of the volumetric system or the pod and panel system of the DfMA house, which are the core modules. The services systems, fittings and white goods will be fitted into the pod units before delivering to the site (Figure 5). Although the pod layouts have a standardised design, customisation is still available as different configurations can be applied to the bathroom and kitchen suites. The installation process is designed to allow feasible and practical assembly on-site, with low labour demands and effort. A plug and play system is adopted to integrate lighting and electricity to the central pod units, which only requires mains supply connection.
Figure 5: Central Pod Layout (Source: Northmill, 2019)
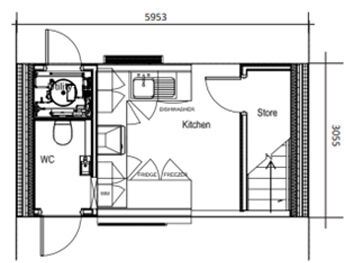
Ground floor pod layout
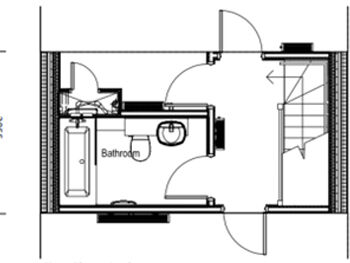
First floor pod layout
4) DfMA House Wall Panel Units
All wall panel units are manufactured on a single production line containing various stations for different installations (i.e. frame assembly, cladding system, windows and doors etc.). Through the single production line, various typologies of DFMA houses can be accommodated for (i.e. detached, semi-detached and terrace). Ultimately, the wall panel units are designed to meet worst-case scenario requirements for climatic conditions as a precaution to overcome global uncertainty. Furthermore, once manufacture is complete, this will lead to robust wall panel units with high internal strength, which enables safe and secure storage. These components are to be stored in a way that makes it easily identifiable and practical to load onto transportation for delivery onsite.
Design for Assembly
Design Criteria
DfMA house addresses the logistical challenges associated with restricted area and small space. Three criteria in relation to assembly are: (i) Accessible transportation; (ii) Minimisation of site storage; (iii) Ease of assembly.
Design solution
- Transportation:
The panel and pod units are specifically designed to minimise delivery issues and logistical constraints during transportation. For example, to deliver a detached DfMA home, only five articulated lorries with a standard size of 13.2m by 2.55m are required.
Site storage:
A Just-In-Time method is adopted as DfMA components are only dispatched when assembly is required. It does not compromise any land space, speeds up on-site manufacturing process and minimises risk of damaging components during onsite delivery. To ensure safe delivery on-site, all components are to be wrapped with thick gauge polythene sheet and sealed with tape, to safeguard against moisture penetration and avoid negative time and cost implications as a result of weather damage.
- Assembly:
To assist with the assembly process of the DfMA house, the wall panel units are supplied with lifting cleats, so they can be craned into position and fixed together using standard fixing details.
Design for high performance and low impacts
Design criteria
The platform-based DfMA house is designed in a holistic manner to ensure it has low impacts and high performance in terms of reducing fuel poverty and energy consumption. The design criteria include (i) Adoption of renewable systems and (ii) Meeting target U-values for building elements. Addressing the criteria will provide clean green energy and lower CO2 emissions, thus reducing the dependency on the National Grid and benefiting the local community. The DfMA house shall equip with smart technology to deliver high-energy performance and low maintenance, running costs and energy bills. Home comfort is enhanced as draughts and cold spots are significantly reduced. Overall, homeowners can enjoy more disposable income from low energy bill through the adoption of sustainable energy systems.
Design solution
1) Adoption of renewable systems
Renewable sources and active technologies have been utilised to optimise sustainability and minimise operational costs during the in-use phase. Photovoltaic panels and air source heat pumps are predominantly chosen to achieve cost-effective reductions in building running costs. DfMA house has high air tightness and meet targeted insulation levels, to form ideal conditions for an air source heat pump to run efficiently. Moreover, active technologies have been deployed to prevent overheating. This includes incorporating automatic blinds, pre-programmed to open and close at certain times of the day to reduce internal heat gains. DfMA also contains a remote monitoring system and lighting systems, which are all connected to a central router in the home and then transferred to a cloud space for access.
Heating standards
Energy Systems Catapult (ESC) undertook an analysis and simulation of energy performance go measure the energy consumption, and operational carbon emissions of DFMA houses. Home Energy Dynamics toolkit (HED) is a domestic dynamic system specially designed to simulate house energy performance. This enables feasible improvements to be implemented to the building fabric and heating system to meet emissions, comfort and running cost requirements.
The HED performs simulations to review home energy usage and energy efficiency among three heating standards - gold, silver, bronze, containing alternative low-carbon technologies and design configurations. For instance, the Gold standard incorporating solar panels and a battery system can substantially reduce heating-related electricity consumption; notably, by 83- 86% according to various occupancy profile.
2) Meeting target U-values for building elements
Federated BIM models were shared across all consortium members to allow testing of iterative designs, so continual feedback can be gained, and informative decisions are made regarding sustainability and energy performance of the DfMA house. To ensure high energy efficiency, target U-values (rate of heat loss through building elements such as walls, doors and windows etc.) are lower than Notional Dwelling Specification provided in Approved Document L1A.
For further information
To gain a comprehensive overview of the design aspects of the Platform-based DfMA house, related to Manufacture, Assembly and Performance, download the Platform-Based DfMA House information pack. This includes extensive information of the kit-of-parts industrialised approach, detailing all the key design criteria’s and the associating design solutions to maximise energy efficiencies and performance functionality, whilst keeping whole-life costs to a minimum.